·The low hysteresis of the EVE composites results inlower heat biuld-up during dynamic strains.
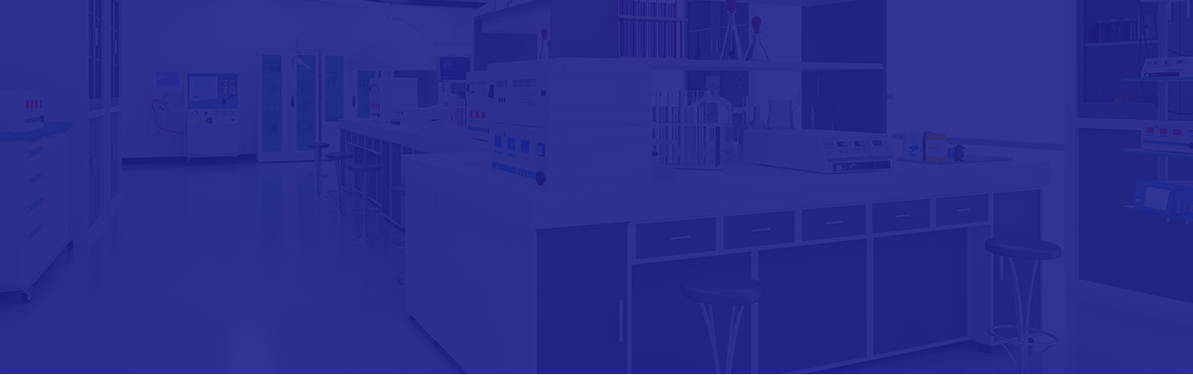
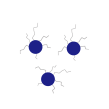
High degree of silylation
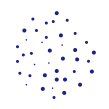
High dispersion of filler
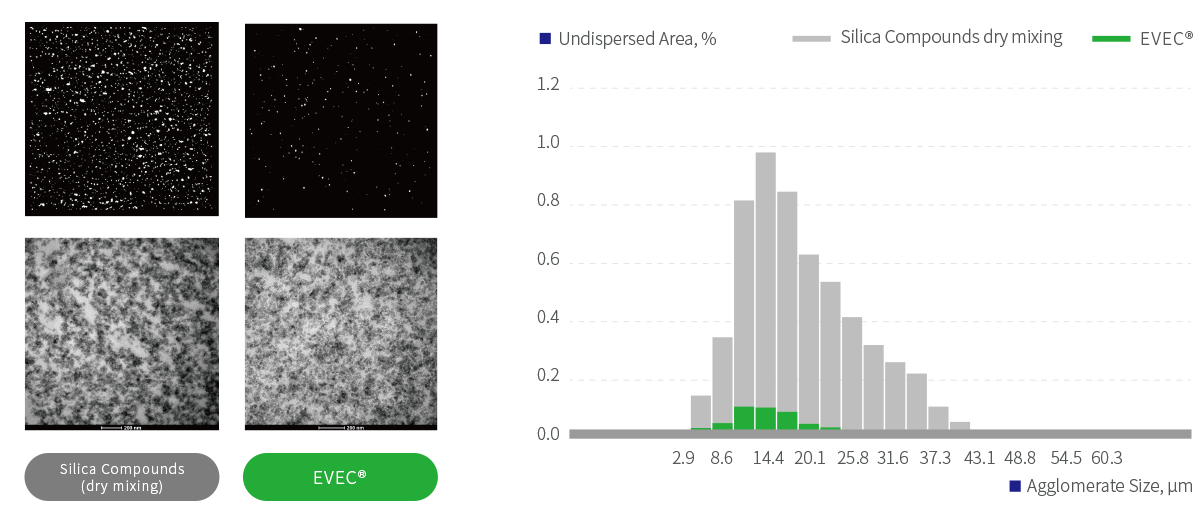
·With the same tormulation,EVEC has ower hardness. n the hardness measurement, the strain involved includes shear, tensionand compression at low strain. lt has been reported that hardness is simply dependent on Young's modulus measured at veryow deformation.
·At such low strain, the filler agglomerates cannot be destroyed, making the modulus higher, The lower hardness of EVECcompounds reflects less agglomeration of the filler aggregates in the polymer.
·The Pavne effect is a particular feature of the stress-strain behavior of rubber containing fllers. The Pavne effect depends on thefiler content of the material and vanishes tor unfiled elastomers. Phvsicallv. the Pavne etect is attributed to detormation-nduced changes in the material's microstructure, i.e. to breakage and recovery of weak physical bonds linking adiacent filleragglomerates.
·EVEC® shows the weakest Payne effect among trial samples, which means it contains the least filler agglomerates.
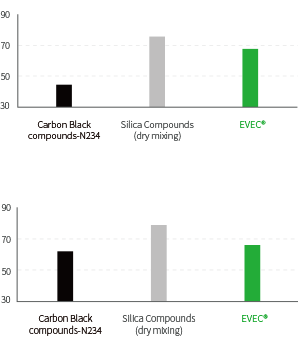
-
Case 1 丨Low Mooney Viscosity
well dispersed, no boundrubber.
-
Case 2 丨High Mooney Viscosity
Poorly dispersed, no bound rubber.
-
Case 3丨 Acceptable highMooney Viscosity
well dispersed with boundrubber.
-
Case 4丨 HighMooney Viscosity
well dispersed, high boundrubber + gel.
·Due to better filler dispersion and higher silane eficiency, EVEC® has ower bound rubber content and Mooney viscosity, the filler/rubber state appearssimilar to case 3.
·For dry mixed silica compounds, more filler agglomerates (case 2) and gel formation (case 4) may be responsible for the higher viscosity.
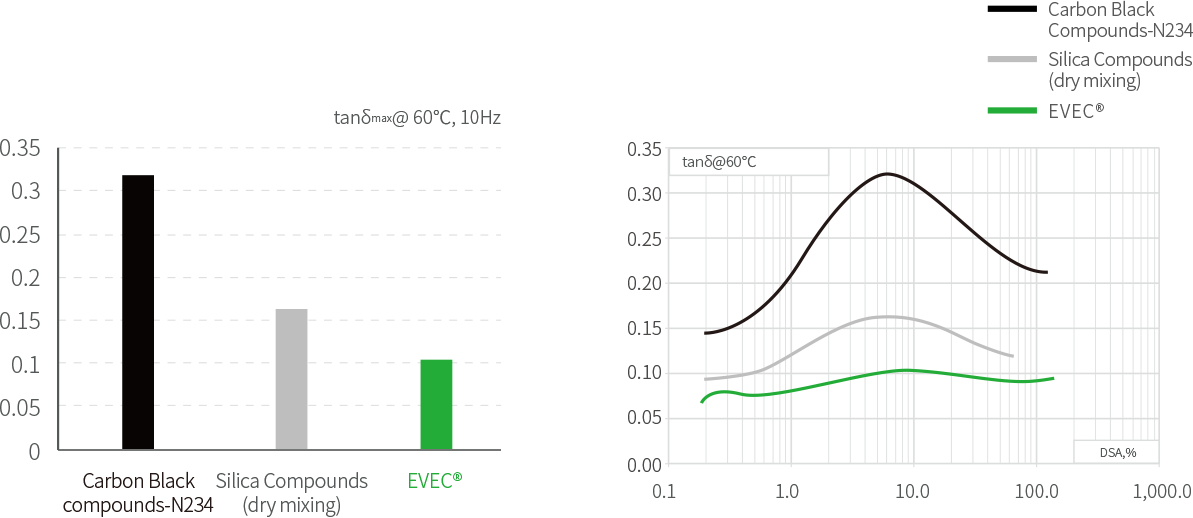
·At high temperatures (such as60°C), the polymer hysteresis in the rubbery state is low. The breakdown and reformation of filler agglomerates causes more energy dissipation during dynamic strain,resulting in higher hysteresis.
·EVEC® with the lowest filler agglomeration has the lowest hysteresis at 60 °C.
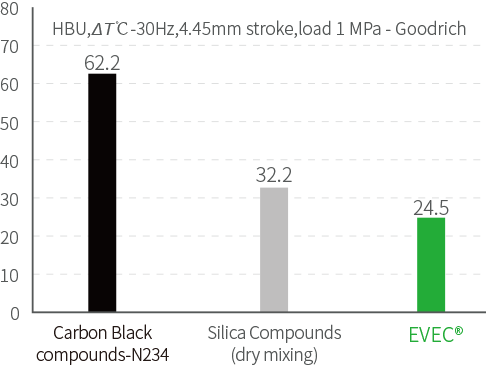
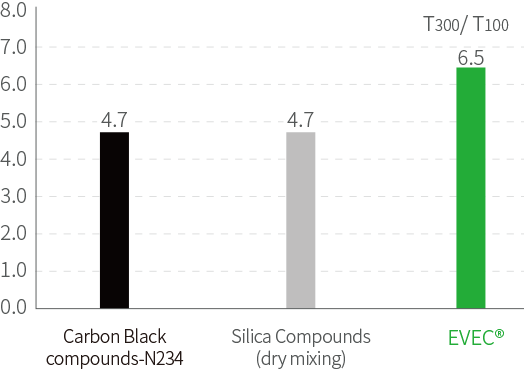
·Among others, the main factor influencing abrasion resistance is polymer-filler interaction. The ratio T300/T100 is used as a measure of polymer-filler interaction and mixing efficiency for a silica coupling agent containing compound. T300 and T100 are thestresses at 300% elongation and 100% elongation, respectively. The high T300 over T100 of EVEC® is beneficial for tire wear resistance.
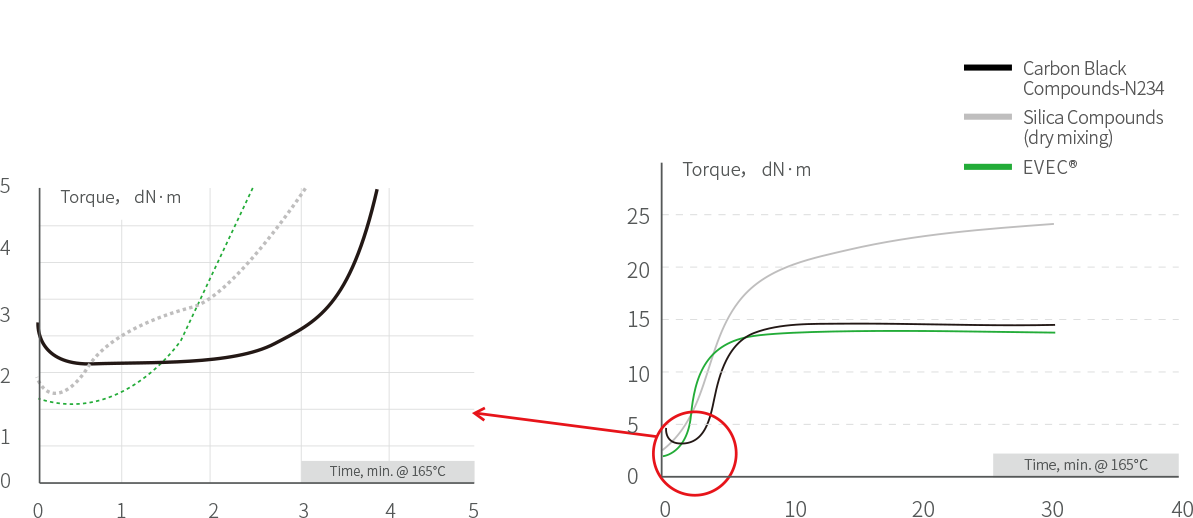
·The marching modulus of the dry mixed compound implies that some coupling agents remain in the polymermatrix continuously forming crosslinks during vulcanization.
·In the case of EVEC®, the flat plateau of the cure curve suggests that almost all coupling agents are attached and/oradsorbed on the silica surface.
·Before the onset ofvulcanization, there is a quick upward curve that is probably due to significant filler flocculation.
·The decreased flocculation in EVEC® is caused by the efective surface modification of the silica since almost all ofthe coupling agent is on the filler surface.
-
Silica Compounds (dry mixing)
-
EVEC®
·Due to less gelation, EVEC® displays better extrusion properties compared to conventional silica compounds. such as lower dice swell and smoother surface.